Preventing Shock with Proper Grounding Techniques
Eighty percent of all power quality problems are found in the electrical distribution and grounding system.
- By Chad Reynolds
- Nov 01, 2003
AN estimated 58 people lose their life each week as a result of electric shock. In an electrical system, the grounding system is the primary protection against electrical shock hazards. It provides a low-resistance pathway to ground to protect against electrical faults. Using proper grounding techniques, testing and maintaining a good electrical ground, and installing protection devices are the best ways to protect people and equipment from electrical shock.
Maintaining a good-quality ground starts with wiring the circuit correctly. The National Electrical Code® (NEC) requires that the removal of any device cannot interrupt the ground path. Receptacle manufacturers have responded by supplying receptacles with only a single grounding connection. This would prohibit electricians from wiring the device in series with the grounding circuit.
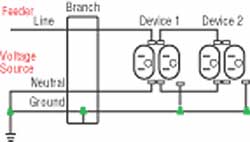
A common method of ensuring the ground remains intact is through the use of a pigtail connection. To make a pigtail connection, take both ground wires and join them with a 6-inch wire of the same color that has been stripped on either end. Hold all three tightly and bind them together with a wire connector. Be sure to use a connector that is the right size for the size and number of wires.
Special connectors are available to make this job easier. With one, a bare copper wire is inserted through a hole at the top of the connector. All the wires are then bound together by twisting the connector until tight. Pre-made pigtails are becoming more popular because of the time savings involved. For example, some connectors now combine a twist-on wire connector with a pre-crimped pigtail. The ultra-flexible, 6-inch lead provides hassle-free positioning in a junction box, and the grounding pigtails come with a pre-crimped fork connection for quick and easy installation of the device.
Bonding the Junction Box to the Grounding Conductor
In many wiring applications, more than one equipment-grounding conductor enters a junction box. According to section 250-1487 of the NEC, where more than one equipment-grounding conductor enters a box, all such conductors shall be spliced or joined within the box or to the box. The only exception is for isolated receptacles, covered in section 250-146 (d), where isolated receptacles are required for the reduction of electrical noise (electromagnetic interference).
For metal junction boxes, the grounding conductors from each device also need to be connected to the box with a listed grounding device, or a grounding screw, that is not used for any other purpose.
Bonding the Receptacle Grounding Terminal to the Junction Box
A device may have to be bonded to the junction box with a jumper. According to section 250-1469 of the NEC, an equipment bonding jumper shall be used to connect the grounding terminal of a grounding-type receptacle to a grounded box unless grounded as in (a) through (d):
(a) A surface mounted box, where the device yoke and the box have direct metal-to-metal contact. This connection can be used to ground the device. This provision does not apply to cover-mounted receptacles unless the box and cover combination have been listed as providing an acceptable ground continuity between the box and receptacle.
(b) Contact devices or yokes designed and listed for providing the grounding connection between the device and the junction box. These shall be permitted in conjunction with the supporting screws to establish the grounding circuit between the device yoke and flush-type boxes.
(c) Floor boxes designed for and listed as providing satisfactory ground continuity between the box and the device.
(d) Isolated receptacles that are required for the reduction of electrical noise on the grounding circuit. In these applications, the grounding terminal is purposely insulated from the receptacle mounting to reduce the electrical noise coming from other loads on the branch circuit.
The receptacle grounding terminal is connected to an insulated equipment grounding conductor run with the circuit conductors. This grounding conductor is permitted to pass through one or more sub-panels without connection to the panel board grounding terminal as permitted in Section 384-2010.
Note that the use of an isolated equipment grounding conductor does not relieve the requirement for grounding the raceway system and junction box.
Maintaining a Low-Impedance Ground
A good electrical ground is more than following NEC requirements; it must also be a low-impedance system. The ground path is the fault path for stray current. If electricity follows the path of least resistance, then the ground circuit must have a lower resistance than an individual to protect him. The rule of thumb for protecting people is to maintain a ground impedance of less than one ohm.
False Grounds
The neutral conductor can only be bonded to the ground conductor at the main neutral bus, where a large copper conductor carries all the return and faulted current back to the earth. Sometimes through error or ignorance, the neutral and ground are connected upstream from the service entrance. This is called a false, or bootleg, ground. If the neutral and ground are connected anywhere else in the building, all grounded metal becomes part of the neutral conductor, constantly energized and creating various voltage potentials on electronic equipment. When you are using common receptacle testers, this condition shows up as normally wired.
Earth Ground
The pathway to ground extends beyond the main panel to the earth ground system. The earth ground could be a single ground rod, multiple ground rods, a mat, or a grid system. Section 250-56 addresses the system by stating that if the ground electrode is not less than 25 ohms, a second electrode should be added at least 6 feet from the first. The grounding system can be tested with a three-pole earth resistance tester or a ground resistance clamp meter.
While testing the resistance of the ground electrode after installation will satisfy NEC requirements, it is not enough to ensure protection for personnel or electronic equipment.
The resistance of the ground electrode is heavily dependent on the soil resistivity. Because soil resistivity relates to moisture and temperature, the resistance of the grounding system will vary throughout the different seasons of the year. To ensure a low impedance grounding system, include the ground electrode or earth ground as part of standard testing procedures in your facility. A ground resistance clamp meter enables electricians to measure the resistance of the ground electrode in a fraction of the time required using the traditional three-point fall of potential test.
Ground Fault Circuit Interrupters
Electrical code requires the installation of ground fault circuit interrupters (GFCIs) in residential dwellings to protect against shock. Receptacles in bathrooms, garages, outdoors, crawl spaces, unfinished basements, kitchens, and near wet-bar sinks require protection.
A GFCI is a receptacle with a built in circuit to detect leakage current to ground on the load side of the device. When the GFCI detects leakage current to ground, it will interrupt power to the load side of the device, preventing a hazardous ground fault condition. These devices should be tested regularly because they rely on mechanical connections that will degrade over time. A recent study performed by the Leviton Institute found on average 15 percent of GFCIs were inoperative when tested. Voltage surges from lightning, utility switching, and other sources take their toll on the devices, which is why Underwriters Laboratories requires that GFCIs be tested monthly.
Equipment Failure
When sensitive electronic equipment fails, the initial reaction is to throw our hands up and blame it on poor power quality. This makes the problem seem unmanageable and out of our control. Most of these problems are actually under our control because 80 percent of all power quality problems are found in the electrical distribution and grounding system.
In addition to preventing the possibility of fire, a good low impedance electrical system will protect electronic equipment. A high-resistance connection, such as a loose wire, will cause the voltage to fluctuate or drop when a large load is applied. If the voltage drops low enough, it can cause electronic equipment to lock up, reset, or shut down completely.
Grounding is another concern for electronic equipment. While ground impedance of one ohm or less may protect people from electric shock, it may not be adequate protection for electronic equipment. The Institute of Electrical and Electronics Engineers Inc. (IEEE) recommends a ground impedance of less than 0.25 ohms for proper protection.
Isolated Grounds and Dedicated Circuits
In some cases, it is easier to isolate sensitive electronic equipment than to rewire an entire circuit. This can be done by running an isolated ground for the equipment in question or by running a new dedicated circuit.
An isolated ground protects the equipment from other equipment on the same grounding circuit. Electronic equipment can create noise, which can interfere with the operation of other equipment on the circuit. It is important to note that an isolated ground will not protect equipment from harmonic distortion running through a shared neutral.
In some cases, running a dedicated circuit is necessary to completely isolate a piece of equipment in order to ensure protection.
A new article in the 2002 code covers the use of transient voltage surge suppressors. These devices protect power, telephone, and cable lines from transient voltage. Transients are short, high-amplitude pulses caused by a release of energy onto the electrical system. These pulses of energy can be caused by internal sources such as a capacitor releasing energy into the system or external sources such as lighting.
Conclusion
The hidden dangers associated with branch circuit wiring are very serious, but fortunately the precautions are straightforward. We can protect ourselves and equipment by using certified devices and testing equipment from reputable manufacturers and by implementing policies on branch circuit testing. These policies should include verifying proper wiring, testing devices, checking the integrity of the branch circuit, and measuring the integrity of the grounding system.
Check all devices immediately after installation to verify proper wiring and test devices. Receptacles should be checked to avoid common wiring errors, such as reversed polarity or an open neutral. Checking the voltage level with a voltage tester quickly verifies the receptacle has been correctly wired for either 120 or 220VAC.
Checking continuity across a switch verifies it works correctly. A variety of testers are available on the market to test these devices quickly and accurately. Test electrical circuits under load to test the integrity of the branch circuit. The voltage drop can identify high-resistance connections, which can lead to fires, breakdown in insulation, and poor efficiency of the electrical system, which can contribute to erratic equipment operation.
Test the integrity of the grounding system, which includes not only the grounding conductors but also the ground rod or grid system. A low impedance on both of these systems is essential to protect against electrical shock.
In summary, branch circuit testing is an important part of wiring any circuit. It verifies devices have been wired up correctly and allows you to protect yourself against the hidden defects in an electrical system.
This article originally appeared in the November 2003 issue of Occupational Health & Safety.