Using PIDs in Confined Spaces
What are you missing in CSE protection?
THE industrial environment has changed substantially since OSHA first defined confined space entry (CSE) regulation in the late '70s, and gas detection regulation has not kept pace. The standard four-gas monitor is simply insufficient protection from the many--now common--toxic gases and vapors that are major constituents or byproducts of modern industrial processes. Monitors that measure only O2, LEL, CO, and H2S are letting common, devastating toxins slip through the safety net, making them insufficient to the task and exposing workers, families, and communities to unnecessary illnesses and deaths.
Writing specifically for sewer entries, OSHA addresses this shortcoming in gas detection in 1910.146, Appendix E:
". . . where the employer has not been able to identify the specific atmospheric hazards present or potentially present in the sewer, broad range sensors are preferable because they indicate that the hazardous threshold of a class (or classes) of contaminants (i.e. hydrocarbons) in the sewer have been exceeded."
In fact, better than 80 percent of the gases and vapors listed in OSHA 1910 Subpart Z--Toxic and Hazardous Substances are volatile organic compounds (VOCs) or hydrocarbons. And because most are toxic long before they are combustible, they go unobserved by the standard four-gas monitor.
PIDs: Accurate, Sensitive Detection of Classes of Toxins
Photo Ionization Detectors (PIDs) measure low levels--0 to 10,000 parts per million--of VOCs, hydrocarbons, and other classes of toxic gases. They provide compact, sensitive, accurate, affordable and reliable real-time gas monitoring of many of the common toxic gases and vapors that four-gas monitors miss.
What are some common VOCs? VOCs are the chemical compounds that keep industry going. They include:
- Fuels
- Oils, degreasers, heat transfer fluids
- Solvents, paints
- Pesticides, herbicides
- Plastics, resins, and their precursors
VOCs are found throughout industry, from obvious applications in the petrochemical and semiconductor industries to not-so-obvious applications, such as sausage manufacturing.
Why Not Use an LEL Monitor?
Many VOCs are flammable and may be detected by the LEL (Lower Explosive Limit) or combustible gas sensors found in virtually every multigas monitor--but not necessarily before they reach toxic levels. As the following chart shows, many common VOCs and hydrocarbons present a serious toxicity hazard at concentrations considerably below their 10 percent LEL alarm limit.
Compound |
LEL by volume |
LEL (ppm) |
10 % LEL (ppm) |
TWA (ppm)* |
TWA in % LEL |
Ammonia |
15 % |
150,000 |
15,000 |
50 |
0.03 % |
Arsine |
5.1 % |
51,000 |
5,100 |
.05 |
0.0001 % |
Benzene |
1.2 % |
12,000 |
1,200 |
1 |
0.008 % |
Diesel |
0.7 % |
7,000 |
700 |
13 |
0.19 % |
Isopropyl Alcohol (Isopropanol) |
2.0 % |
20,000 |
2,000 |
400 |
2 % |
Jet Fuel |
0.6 % |
6,000 |
600 |
35 |
0.58 % |
Methyl Ethyl Ketone |
1.4 % |
14,000 |
1,400 |
200 |
1.4 % |
Styrene |
0.9 % |
9,000 |
900 |
20** |
0.22 % |
Toluene |
1.1 % |
11,000 |
1,100 |
50** |
0.45 % |
Trichloroethylene (TCE) |
8 % |
8,000 |
800 |
100 |
1.25 % |
Vinyl chloride |
3.6 % |
36,000 |
3,600 |
1 |
0.0028 % |
Xylene |
1.1 % |
11,000 |
1,100 |
100 |
0.9 % |
*OSHA 1910 Subpart Z--Toxic and Hazardous Substances
**ACGIH®, 2002 |
For many common compounds, TWA alarm conditions are reached at concentrations several magnitudes lower than LEL. Add to this the fact that LEL sensors typically have an accuracy of +/- 3 percent of the reading, and it is clear LEL sensors do not provide sufficient protection from unanticipated gaseous threats. LEL sensors measure "explosivity," not toxicity.
Measuring in PPM: The Maturation of Gas Monitoring
When "four-gas" confined space monitors first hit the safety market, the goal was to stop fatalities in confined spaces from the acute (immediate) affects of toxic or explosive gases. Simply put, LEL sensors made sure workers got home at night. As gas monitoring needs mature, CSE professionals are becoming increasingly concerned with the chronic (long-term) effects of many gases and vapors.
Detecting at these low levels requires gas measurement tools that measure in parts per million (ppm). Measuring in ppm lets workers enjoy retirement! Used properly, a PID is the best choice to provide workers confidence in many chemical environments.
Confined Space Fatality Reports
Other Advantages
Some say that while the PID is clearly sensitive to many toxic gases and vapors at ppm levels, its lack of selectivity reduces its usefulness. For many applications, that lack of specificity is, in fact, a lifesaver.
CSE technicians who have the right equipment and follow the regulations are protected from the anticipated dangers--lack of oxygen, threat of combustion, hydrogen sulfide or carbon monoxide poisoning. The advantage of the PID is that it is not selective; able to detect a broad spectrum of VOCs and hydrocarbons, it is a highly portable, continuous-operation monitor that provides immediate feedback to workers concerning unseen and unanticipated threats. This lets them take control of their actions and lets them perform their job tasks with the confidence that they are not being exposed to hazardous chemicals. The PID measures continuously and results can be stored and "played back," instantly.
Adsorbent tubes respond slowly to changes in concentration. This means they can miss, or grossly underestimate, some exposures. For example, suppose a worker's task involved periodically leaning into a degreasing machine. While leaning into the machine, the worker was exposed to 300 ppm of perchloroethelyne for 10 seconds. This quick exposure certainly has toxic affects on the worker, but the slow response of adsorptive sampling techniques, coupled with their averaging, may completely miss this practice. A PID not only could datalog these quick, high transient responses, but it can provide alarms to alert the operator to this unsafe procedure.
PIDs provide instantaneous alarms so workers can take immediate action. Chemical vapor safety is no longer delivered in a disciplinary manner by an industrial hygienist; instead it is a proactive part of the workday. Adsorptive techniques are reactive rather than proactive; by the time the data is available, the worker has already been exposed.
How Does a PID Work?
A PID uses an ultraviolet light source to break down chemicals into positive and negative ions that can easily be counted with a detector. The detector measures the charge of the ionized gas and converts the signal into current. The current is then amplified and displayed on the meter as "ppm." After measurement, the ions reform the original gas or vapor. PIDs are non-destructive; they do not "burn" or permanently alter the sample gas, which allows them to be used for sample gathering.
Ionization Potential
All elements and chemicals can be ionized, but they differ in the amount of energy required to cause ionization. The energy required to displace an electron and "ionize" a compound is called its Ionization Potential (IP), measured in electron volts (eV). The light energy emitted by a UV lamp is also measured in eV. If the IP of the sample gas is less than the eV output of the lamp, then the sample gas will be ionized.
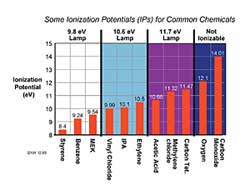
IPs can be found in the NIOSH Pocket Guide, PID manufacturer literature, or in many chemical texts.
What Does a PID Measure?
The largest group of compounds measured by a PID is the organics--compounds containing carbon (C) atoms--including the following:
- Aromatics. Compounds containing a benzene ring, including benzene, toluene, ethyl benzene, and xylene.
- Ketones and Aldehydes. Compounds with a C=O bond, including acetone, methyl ethyl ketone (MEK), and acetaldehyde.
- Amines and Amides. Carbon compounds containing nitrogen, such as diethylamine.
- Chlorinated hydrocarbons. Trichloroethylene (TCE), perchloroethylene (PERC).
- Sulfur compounds. Mercaptans, sulfides.
- Unsaturated hydrocarbons. Butadiene and isobutylene.
- Alcohols. Isopropanol (IPA) and ethanol.
- Saturated hydrocarbons. Butane and octane.
In addition to organic compounds, PIDs can be used to measure some inorganics, which are compounds without carbon. They include:
- Ammonia.
- Semiconductor gases. Arsine, phosphine.
- Hydrogen sulfide.
- Nitric oxide.
- Bromine and iodine.
What PIDs Do Not Measure
- Radiation
- Air (N2, O2, CO2, H2O)
- Common toxics such as CO, HCN, SO2
- Natural gas (methane, ethane)
- Acid gases (HCl, HF, HNO3)
- Others--freons, ozone (O3), hydrogen peroxide
- Non-volatiles: PCBs, greases
PIDs are now capable of measurements from 0 to 10,000 ppm with resolution as low as 1 ppb (parts per billion). They are a powerful means of detecting and measuring VOCs and other toxic gases and vapors at concentrations far lower than LELs.
PID technology, coupled with the standard four-gas monitor, provides CSE professionals powerful, affordable, portable protection from unanticipated as well as anticipated threats. The PID's ability to provide accurate "broad band" detection of a host of common, highly toxic compounds makes it a necessity in today's modern industrial environment.
References
1. NIOSH: Pocket Guide to Chemical Hazards, NIOSH Publications, Cincinnati, OH 19942.
2. DHHS (NIOSH) Publication No. 79-142, 20023.
3. Worker Deaths in Confined Spaces--A Summary of NIOSH Surveillance and Investigative Findings, January, 1994, DHHS (NIOSH) Publication No. 94-103
4. OSHA 1910 Subpart Z--Toxic and Hazardous Substances
5. Guide to Occupational Exposure Values--2002, compiled by ACGIH
6. NFPA 325, Guide to Fire Hazard Properties of Flammable Liquids, Gases, and Volatile Solids, 1994 Edition
7. RAE Systems: Correction Factors and Ionization Potentials (Technical Note TN-106)
8. RAE Systems: AP-211: PIDs for Continuous Monitoring of VOCs
Confined Space Fatality Reports
Could these lives have been saved if a PID had been used in conjunction with a standard four-gas monitor?
- Two workers were poisoned while cleaning an aluminum trailer tank with a phosphoric acid solution. The tank had been used six months previously for the transport of a 42 percent solution of sodium arsenite (weed killer). Since that time, it had been cleaned with steam and detergent and used for storage and transportation of alcohol and other industrial solvents. Before assigning the trailer to another client, a thorough cleaning job was ordered, which required the hand application of the acid cleaner. Subsequently, arsine was generated by a reaction between the acid cleaner and the aluminum, which had arsenic impurities.
- Three contract workers died while repairing the interior rubber lining of a sodium hypochlorite tank at a wastewater treatment plant. The workers were working in a confined space, using extremely toxic and flammable chemicals (toluene, xylene, methanol, isopropanol, and methyl ethyl ketone). Because the workers did not have an atmospheric gas testing instrument, the plant maintenance engineer provided one capable of detecting oxygen, flammability, and hydrogen sulfide. Two days later, the workers were found dead inside the tank. The medical examiner listed the cause of death for all three workers as toluene poisoning.
- Three workmen were cleaning out a trichloroethylene degreasing tank. The tank is cleaned out only when the plant is not in operation; therefore, only the three assigned to the cleaning task were in the plant. A relative of one of the workers stopped by the plant that evening and found all three workmen down in the tank and unresponsive. One was dead when removed, one died a few hours later at a local hospital, and one remained critical for a month and then died without regaining consciousness.
- A 34-year-old male painter died when he apparently inhaled vapors from paint containing xylene, lost consciousness, and fell 140 feet within the vertical water supply pipe of a municipal water tower.
This article originally appeared in the February 2004 issue of Occupational Health & Safety.