Orbital Intervention
[<p>Simulation prevented CO<sub>2</sub> accumulations from endangering occupants of an out-of-this-world workplace: the International Space Station.</p>]
- By Chang Hyun Son, Ph.D.
- Jul 01, 2004
COMPUTER simulation is helping to protect astronauts on board the International Space Station from carbon dioxide buildup when the crew quarters ventilation system is out of service. Astronauts on the space station sleep in small compartments or crew quarters that are equipped with doors and ventilated with fans. The concern exists that if the fans were to stop operating, carbon dioxide could build up to potentially dangerous levels.
In the past, engineers addressed this type of environmental issue using single-node simulation software, which has the weakness that it provides only average concentration values for an entire compartment. This makes it impossible to determine whether dangerous concentrations exist in certain areas of the compartment even though the average levels are acceptable.
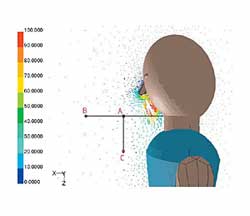
Engineers overcame this problem by using computational fluid dynamics (CFD) to predict carbon dioxide concentration in every area of the cabin. The simulation determined that when the fan was turned off for a certain period, dangerous levels of carbon dioxide indeed occurred in the crew quarters. These results, which would have been very expensive to duplicate experimentally, have brought about the creation of rules that provide for astronaut safety in situations when the fan is out of service.
ISS Life Support Systems
The ISS Environmental Control and Life Support System (ECLSS) is designed to take the place of Earth?s natural life support system by providing air, water, and other necessities for life in space. Oxygen is supplied by electrolysis of water, and potable and hygiene water is recovered from wastewater. These and similar advances help to reduce the cost of operating the space station by reducing the need to provide fresh supplies and to return used equipment to earth. Distributing these necessities of life throughout the crew-accessible areas of the space station is another vital function of the ECLSS.
There are six crew-accessible areas in the ISS service module: the transfer compartment, working compartment, transfer tunnel, two crew quarters, and the bathroom facility. Crewmembers sleep in the crew quarters in sleeping bags attached to the walls that prevent them from floating through the cabin and bumping into walls while they are sleeping. An air conditioning system and a network of ducts ventilate the service module.
The Need to Prevent CO2 Buildup
Each of the two crew quarters has a fan that can be turned on and off with switches located inside. The crew can choose a range of airflow from 20 to 170 cubic feet per minute. The crew quarters are equipped with doors that are ventilated to allow air to travel back to the cabin when the doors are shut.
The concern exists that, in the event a crew quarters fan were to stop operating, carbon dioxide exhaled by the crewmember would build up to excessive levels. A peak level of 7.6 mm Hg partial pressure is allowed under normal station conditions and can be experienced without any ill effects. A level of 15.0 mm Hg is considered to be the danger threshold, and early mission termination is planned if carbon dioxide cannot be maintained below this level. A level of 30.4 mm Hg is immediately dangerous to life and health, although no escape-impairing or irreversible health effects are seen for exposures of less than 30 minutes.
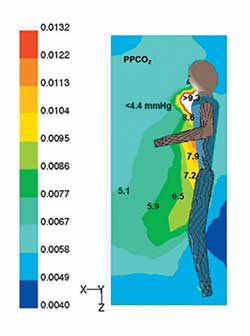
In the past, engineers have used single-node codes to model the ISS environment. One basic limitation of these codes is that they cannot model airflow within a cavity, so they must assume uniform temperature and species concentration. This simplification was not acceptable in this application because high concentrations of carbon dioxide near the crew members can be dangerous even if average levels within the crew quarters are acceptable. In addition, physical testing was clearly unacceptable because of the potential dangers involved. For these reasons engineers turned to CFD, which provides fluid velocity, temperature, chemical species concentrations, and other relevant variables throughout the solution domain for problems with complex geometries and boundary conditions.
As part of the analysis, a researcher can change the system geometry or the boundary conditions and view the effect on fluid flow patterns, temperatures, or the distributions of other variables, such as the concentration of carbon dioxide in the present study. In this instance, the software's graphical user interface greatly reduces the amount of time and training required to set up the analysis, and its parallel processing capabilities take full advantage of multiple processor workstations or networks of workstations to reduce computation time.
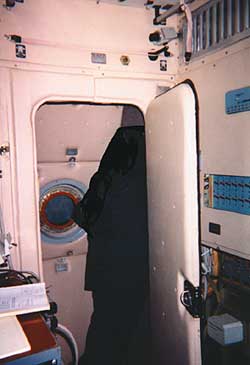
The CFD model was built to represent the ventilation configuration within one of the crew quarters. The region was modeled as an enclosed cubic volume with an inlet for air at one end and an outlet at the other end. The doors in the model can be simulated in either an open or closed position. A human model acts as a carbon dioxide source within the quarters. The characteristics of the model were based on a sleeping crewmember's generating 1.4 pound per day of carbon dioxide, as well as literature stating that expired air is about 3.6 percent carbon dioxide.
A CFD model with more than 500,000 tetrahedral cells was generated. A steady-state flow field was obtained and used as the initial airflow distribution for the subsequent transient calculation where the spread of CO2 was tracked. Boundary conditions were selected to represent flow adjacent to the walls of the module interior and flow streams into and out of the module at the supply and return registers. The boundary conditions for the air inlets were considered as velocity inlets with appropriate magnitude and direction relative to each inlet plane. Then governing equations for mass, momentum, and species concentration were solved.
Results: CO2 Buildup When Fan is Off
The CFD results showed that approximately 22 percent of the volume of the crew quarters had an air velocity in the range of 15 to 40 fpm, and 36 percent of the volume is below 7 fpm when the ventilation is on and the compartment is occupied. Time history plots of carbon dioxide concentration were generated at three locations near the face of the crewmember. Two locations are 8 and 16 inches in front of the chin of the human model. The third is 8 inches in front of and 8 inches below the chin.
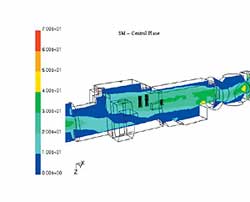
The CFD results showed a steady buildup of carbon dioxide over time when the fan is off. The partial pressure of carbon dioxide starts at 3.0 mm Hg when the fan is running. When the fan is shut down, the carbon dioxide concentration rises to 4.6 mm Hg in the first location, 4.4 mm Hg in the second location, and 5.3 mm Hg in the third location 10 minutes after ventilation ceases. The carbon dioxide concentration throughout the entire crew quarter ranges from 3 mm Hg to 9.3 mm Hg at the same time. Over time, the simulation showed concentration would continue to rise as the crewmember inhales and exhales air with increasing carbon dioxide content, to 11.6 mm Hg after one hour of elapsed time. The results further show that opening the door of the crew quarter only slightly reduces the rate at which carbon dioxide concentration rises.
The CFD simulation showed that carbon dioxide concentration within the crew quarters quickly rises above acceptable levels when the fan is turned off. The simulation was also run with the assumption of perfect mixing and showed that the average partial pressure of carbon dioxide was only 4.4 mm Hg after 10 minutes.
This demonstrates the advantages of CFD over the single-node codes, which would have severely underestimated the danger caused by carbon dioxide buildup in the crew quarters. The simulation results were used to propose rules for use of the crew quarters in the situation where the fan is out of service. The authors of the study also suggested that carbon dioxide sensors be deployed in the crew quarters to further reduce the risk of injury caused by any failure of the ventilation system.
This article originally appeared in the July 2004 issue of Occupational Health & Safety.