Proper Emergency Equipment Selection
. . . there's more to it than meets the eye!
- By Casey Hayes
- Oct 01, 2004
A high-pressure pipe bursts or a barrel falls off of a forklift. An accident can happen in an instant! Thousands of industrial and commercial accidents occur each year involving airborne particles and chemicals such as corrosives (acids and bases), oxidizers, and solvents. In hazardous environments, the first line of defense is Personal Protective Equipment, such as gloves and goggles. But as we all know, accidents still happen.
To mitigate further injury, ANSI guidelines call for ready access to emergency equipment, including eyewashes, eye and face washes, and drench showers. These important pieces of equipment are tasked with diluting and/or removing hazardous materials from contact with victims' bodies. However, because of the virtually unlimited combination of hazardous materials, applications that use them, and other complicating factors--such as facility size and layout, selection of equipment type, and specific features--selection of equipment type and specific features are left up to the specifier. This rather nebulous circumstance often leaves specifiers wondering about the "right" choice for their application.
Many people feel there is little difference between the various brands and models of eyewashes, eye/face washes and drench showers. This, however, couldn't be further from the truth. Proper selection is a function of knowing your risks, the characteristics of the materials you work with, and logical consideration of the variety of available products and design configurations.
As with any commercial product, emergency equipment design is a balance between the desire for specific features and capabilities weighed against costs. Features such as pressure compensating flow controls, diffused and/or otherwise cushioned flushing fluid outlets, and heavy-duty componentry may be more expensive but well worth it in a given application.
ANSI Standard Z358.1-2004 provides a guide to aid manufacturers, specifiers, and the general public relative to emergency eyewash and shower equipment. It also advises those concerned with compliance to obtain local medical input regarding risks and countermeasures. This review is not meant to be an interpretation of the standard, nor is it intended to replace the advice of a competent medical professional. Instead, the following information is aimed at developing a logical thought process that comprehends your specific circumstances and considers the various alternative product features and designs.
Recognize Your Risks
You should start with a clear understanding of your risks. Consider the materials your employees handle, the degree of hazard those materials represent, and the likelihood of spill or splash accidents involving employees or others:
- How harmful are those materials, and how likely is an accident?
- Are Personal Protective Equipment elements provided, such as aprons, gloves, and goggles?
- In the event of an accident, are emergency equipment facilities available within 10 seconds of potential accident sites, with unobstructed access? Are they located on the same level as the potential accident sites?
- Are your employees aware of--and practiced in the use of--safeguards, first aid, and countermeasures?
- Are showers, eyewashes, and eye/face washes properly maintained and regularly tested?
- If you are working with a new installation or a renovation, do you have adequate emergency equipment locations? Remember to consider the possibility of multiple injuries from a single accident. Are emergency facilities properly located? Properly signed and visible? Are they readily accessible to injured workers?
- Do you need drench showers, eyewashes, eye/face washes, or combination units? This can be a reasonably challenging question. Consider the hazardous materials in use. If large portions of the body could possibly be exposed to hazardous materials, a shower is definitely indicated. In smaller scale incidents, a single drop of caustic material, for example, might splash on a countertop and bounce up into an employee's eye. This would probably require an eyewash. Likewise, many airborne contaminants might irritate the eyes only, again with an eyewash being the answer. However, don't forget that one of the main functions of emergency equipment is to dilute the hazardous substance. Larger scale spills and splashes of hazardous materials that could cause injury to the face, as well as the eyes, would naturally drive the need for eye/face washes. Most safety professionals agree one should err on the side of caution with respect to both the types and number of pieces of equipment.
Consider Your Alternatives
Drench Showers
Let's begin by looking just at drench showers both as stand-alone products and combined with either eyewashes or eye/face washes. ANSI Z358.1 establishes a sustained flow benchmark of 20 gpm, with a diffused spray pattern that maintains a 20-inch width at a height of 60 inches above the ground. Photo 1 shows two combination shower eyewashes side by side. The left side unit shows a proper pattern width and height. The right side unit shows a typical non-compliant shower pattern. Note the columnar flow of the older style shower, which would require an injured person to move around under the flow to even come close to attaining a proper drench pattern. Older style showers with columnar flow patterns should be replaced and non-compliant alternative products should be avoided.
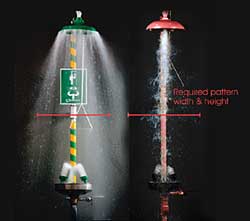
|
Photo 1 |
Eyewashes and Eye/Face Washes
There are a wide variety of eyewash and eye/face wash products available, depending on specific needs and budgets. The following capsules will contrast popular features and benefits.
Flow "Softness": Photo 2 shows a conventional eye/face wash in operation with the water flow from an eyewash overlaid on it.
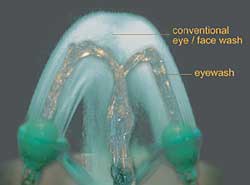
|
Photo 2 |
Beyond coverage area considerations, proper flow characteristics are generally the same. Notice the softness of both flows. Neither one is excessively high, nor does either give the impression the water pressure would be high enough to be uncomfortable to the user. Consider the height of the flow. Per ANSI Z358.1, from the peak of the flow to a point 1.5 inches lower, the flushing fluid pattern should adhere to the ANSI test gauge protocol. If the pressure and height of the flow are too high, the accident victim might shortcut the required irrigation time. If they are too low, the effectiveness of the irrigation cycle might be compromised. This is an important point.
Also, pay close attention to the design of the spray nozzles. While perhaps not as important in eyewashes, eye/face washes often must flow significantly more water. This should drive the use of a diffused design to cushion the flow as much as possible.
Flow Height, Spray Pressure and Angle of Approach: As stated earlier, there are many different eyewash and eye/face wash products on the market, with various designs, operating features, and price points. Consider your alternatives carefully. Look for features such as effective dust covers, designed so they don't obstruct the drain when in use. Two often overlooked features are a pressure control valve and flow compensating device. Photo 3 shows the conventional eye/face wash seen earlier, which features a pressure control valve and flow compensating device. For illustrative purposes, we have overlaid the flow of a competitive eye/face wash without these features. Consider the level of comfort likely to be encountered by a victim who must immerse his or her face into the streams.
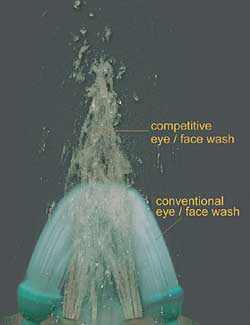
|
Photo 3 |
Photo 4 shows an example of the dramatic difference between certain products, with respect to the angle of approach of the flushing fluid. Logic dictates the best angle of approach in flushing the eyes would be straight on with a soft flow that contacts the entire eye simultaneously. Approaching the eye from a severe angle would seem to leave a portion of the eye not directly contacted by the flushing fluid flow. Once again, consider the victim's level of comfort during use and the likelihood of his using the equipment for a full 15-minute cycle.
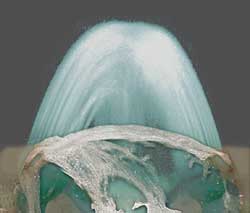
|
Photo 4 |
Maximum Coverage Eye/Face Washes: When an eye/face wash is required, one also should consider the coverage area afforded by your ultimate product selection. As was illustrated earlier, the coverage difference between an eyewash and an eye/face wash is significant. Specifiers also should be aware there are high-coverage eye/face washes available. These products can provide about five times the coverage of a conventional eye/face wash in a package of about the same overall dimensions and relative cost. Photo 5 shows a straight-down-from-above composite view of a standard eyewash flow overlaid onto a conventional eye/face wash flow overlaid onto a high-coverage eye/face wash flow. The differences are dramatic and provide welcome news to those applications that require them.
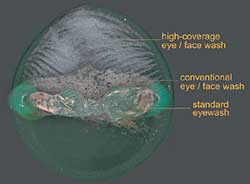
|
Photo 5 |
Combination Showers and Eyewashes
Simultaneous Use
Assuming one has specified equipment with the best flow patterns and coverage, another very important feature of combination shower/eyewashes and shower/eye-face washes is flow controls. Flow controls maintain a stable supply of flushing fluid during simultaneous use of the shower and eye or eye/face wash. For illustration purposes, Photo 6 is a tighter version of the comparison shown in Photo 1, centering now on only the eyewashes. The combination unit on the left has flow controls, and the one on the right does not. Note the significant decrease in flow of the eyewash on the right during simultaneous use. This difference can often result in the eyewash or eye/face wash falling below the ANSI minimum flow height.
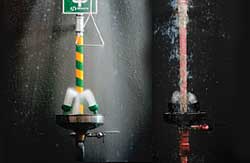
|
Photo 6 |
Summary
When we design and specify emergency equipment installations, we sincerely hope they are never needed. However, the reality is they probably will be used, no matter how safety-conscious a company may be. So, we logically seek out the best products, place them in the most appropriate places, and diligently train employees to ensure the maximum safety net is provided.
As we've shown, there are differences in products that make some better for specific applications than others. And, as always, budget plays an important part in the selection. In the end, specifying becomes a balancing act--balancing features and capabilities against cost. The best way to deal with a balancing act is to know all of the facts!
This article originally appeared in the October 2004 issue of Occupational Health & Safety.