Working Safely with Beryllium Oxide
This facility used no special PPE in its production operations and employed housekeeping as an administrative control in most areas as part of the process.
- By Michael Berakis
- May 01, 2009
Beryllium is the fourth element in the periodic table. It comes right after lithium and before boron. It's a metal that looks like aluminum but is lighter and stronger. In ceramic form, beryllium oxide (BeO) conducts heat but not electricity and has the highest thermal conductivity of commercially available ceramics. It is used in everything from wireless base stations to satellites and advanced radar systems.
Beryllium oxide can be used safely. BeO has been and continues to be used safely. For many years, the primary beryllium manufacturer has effectively utilized engineering controls and work practice controls with dramatic results. (See the Beryllium Worker Protection Model sidebar on page 36.) Our company is demonstrating that new cases of chronic beryllium disease can be successfully prevented in the primary manufacturing industries where there had been a risk.
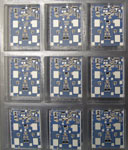 |
Figure 1. Thick film metallization operations have a potential for generating measurable airborne beryllium. |
For other users, any potential risk is very manageable. Many industries have been working safely with BeO ceramics for a long time; this article will highlight one such operation.
Brush Wellman has initiated a series of studies to document industries that have been working safely with BeO ceramics. We wanted to add to our knowledge base of safe practices and also communicate to others in the industry that BeO ceramics are already being used safely. As part of this initiative, we conducted a study at a microelectronics facility currently using BeO substrates and evaluated operations and tasks commonly associated with circuit assembly and production. The manufacturer studied produces printed circuits on BeO ceramic substrate (as shown at left).
Using beryllium doesn't necessarily mean worker exposure to beryllium. Based on an initial qualitative assessment, six production areas in the plant were identified where operations could involve the generation of BeO particulate and therefore potentially require the use of engineering and work practice controls to ensure worker protection. The areas were the metallization area, the reflow/brazing area, the testing area, the wire bond area, the firing room, and lid removal. The production operations studied were divided into eight similar exposure groups: thick film metallization, reflow, wire bonding, brazing, laser resistor trimming, firing, die attach, and material handling operations. Maintenance personnel were also evaluated based on the potential to generate airborne beryllium particulate during maintenance on equipment and other non-routine tasks.
It should be stressed that due to the nature of the operations, we believed it to be unlikely we would find any measurable airborne beryllium over the California PEL (permissible exposure limit) of 0.2 micrograms of beryllium per cubic meter of air (alevel that has been demonstrated to be effective in presenting health effects). This microelectronics facility was not processing the beryllium oxide circuit board material in ways that was likely to cause beryllium oxide to be released. This operation and many others we're in the process of characterizing are typical of downstream users: They use beryllium products but don't create measurable airborne beryllium particulate. Also, at this downstream beryllium oxide user, in addition to a low potential for airborne beryllium, most operations already required controls, such as dust masks, to protect the product or ventilation to prevent workplace exposures to metallizing pastes. These common controls serve to further minimize any potential exposure to occupational dusts generated during the processing of circuit boards. The facility used no special personal protective equipment for beryllium in its production operations and employed housekeeping as an administrative control in most areas as part of the process. Maintenance operators were required to use half-mask respirators when servicing any dust collection equipment, but that was the only operation requiring personal protection.
The results of the study revealed the controls used at this facility were more than sufficient to maintain beryllium levels well below the California PEL.
Sampling Results
Sampling showed all workers were protected. During the study, 73 samples using filters attached to the workers' lapels were collected, and another 37 filter samples were collected not on the workers, but in the general areas identified above, close to where the workers were located. With our analytical ability, we were able to detect as little as 0.007 micrograms of beryllium on a sample and collected over a cubic meter of air on all of the samples. Out of 110 samples collected, only two samples detected any beryllium at all, and these samples were well below the California PEL.
A closer look reveals why. Of the eight operations sampled, we chose to focus more closely on three of them. These were processes that we felt, prior to sampling, had the most potential for generating measurable airborne beryllium. These operations were thick film metallization (see Figure 1), laser resistor trimming, and lid removal.
The thick film metallization operation has no engineering controls and reported the accumulation of visible particulate on the work surface during loading. This operation had one lapel sample just above the 0.007 microgram detection level during the first day of the survey. After detecting beryllium in the first sample, the recommendation was made to clean the equipment after each set of parts was run. This prevented the accumulation of particulate, and no further detectable air sample results were measured during the study of this operation. This is an example of keeping the work area and processes clean, part of the Beryllium Worker Protection Model.
The second of the three processes we focused on, the laser resistor trimming operation, was performed using a Class 4 laser in an active trimming process. The laser operation has the potential to generate airborne particulate by inadvertently removing a very small amount of the beryllium oxide substrate. Normally, however, any surface removal of the BeO substrate is minimized to avoid damaging the metallization or substrate (see Figure 2). As is standard industry practice, the laser process is enclosed to prevent operator exposure to the laser. The operation also was ventilated to a central collection system to remove any metallization fume generated by the process. The operator would access the process only to load and unload parts. Under these conditions, the airborne beryllium concentration from laser resistor trimming operations was not detectable. This is another example of a BeO user's already employing an element of the Beryllium Worker Protection Model (i.e., keeping beryllium at the source) as part of its normal operations.
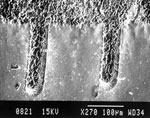 |
Figure 2. The grain structure of the trimmed area of the BeO substrate is equivalent to the surrounding area, indicating no material removal. |
Lid removal was the third closely studied task. In this operation, the operator uses an abrasive wheel to cut the lid from the finished package. The operation is used to rework product that has failed in testing. Because an abrasive wheel is used, it was believed the process had some potential to generate particulate. The operation has local ventilation in the form of a HEPA vacuum. Air samples from this operation also showed no detectable level of beryllium.
Summary
At the facility studied, only two air samples out of 110 were above the detection limit, and none was close to the California PEL. Even though we found no beryllium levels close to the PEL, the facility could still easily make a number of changes that would add extra assurance it is not likely to find measurable levels in the future.
Some would require extra work, to be sure, and there could be some limited expense. However, if you are working with BeO, chances are you are already doing many of them and, in many cases, other industrial materials will require similar controls. We think most of our downstream users will have similar results, and we plan further case studies to demonstrate it to everyone.
This article originally appeared in the May 2009 issue of Occupational Health & Safety.