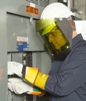
Managing Risk as a Fundamental Business Process
Electrical workplace safety deficiencies are among the top 10 violations most frequently cited by OSHA.
- By Joseph Weigel
- Sep 01, 2011
In his book "The Practice of Management" (1954, Harper and Row, New York), noted business management consultant Peter Drucker stated: "The first duty of business is to survive. The guiding principle of business economics, in other words is not the maximization of profit, it is the avoidance of loss."
Safety is a business process and should be managed with the same diligence as financial, quality, and production processes. From a return-on-investment perspective, there is strong evidence that being committed to safety produces measurable returns on the investment required. The investment for electrical safety compliance must be planned. In order for corporate safety programs to succeed, there must be a commitment from senior management to a strongly communicated, financially supported safety process that achieves measurable results.
A report issued by OSHA's Office of Regulatory Analysis stated, "our evidence suggests that companies that implement effective safety and health programs can expect reductions of 20% or greater in their injury and illness rates and a return of $4 to $6 for every $1 invested."
The Hazards of Electrical Work
Electrical work is a particularly hazardous activity, and this fact has been well documented in the accident statistics for more than 100 years. Electrical hazards fall into two categories: electrical shock and injuries from arc flash events. Arc flash and arc blast accidents often result in very serious burn injuries and physical trauma from arc blast pressure. Both shock and arc flash injuries are often fatal and, even when survived, often result in long-term health issues.
Electrical work is routinely performed in almost every kind of business facility, whether by staff employees or outside contractors. OSHA enforces workplace safety requirements for all private-sector employers. OSHA cites to its own requirements, as well as the requirements for electrical workplace safety contained in the NFPA 70E® Standard for Electrical Safety in the Workplace.
Electrical accidents that result in a fatality or injury always require investigation by OSHA. The responsibility for safety belongs to the company that owns the equipment, regardless of who is actually performing this hazardous work. Electrical workplace safety deficiencies are among the top 10 violations most frequently cited by OSHA.
Electrical Injuries and Their Human Consequences
Five to 10 times per day in the United States, a worker is severely injured or killed in an electrical arc flash accident. Approximately once per day, a fatality is recorded from an electrical arc flash accident. Other electrical incidents also can injure workers; these typically involve accidental contacts with energized components or energized cables that result in shock and electrocution. The injuries and fatalities that result from these accidents are always devastating to the workers and their families. Additionally, the financial consequences of such events can be very damaging to the employer and its insurers.
The human consequences of serious electrical accidents are always tragic. These accidents affect not only the employee(s) involved, but families as well. If the employee survives a serious accident, the extent of his or her injuries often means the employee might never be able to return to work. The physical trauma affects not only the employee's future quality of life, but also, in many cases, life expectancy is significantly shortened as a result of the traumatic injuries.
There are important steps that companies can take to reduce or even eliminate the occurrence of electrical accidents and better protect the worker and the employer from the physical, financial, and statutory consequences of electrical accidents. Most of these steps are contained in the NFPA standard 70E 2009, which provides a detailed reference for facilities to meet the requirements of electrical workplace safety.
Clearly, the fundamental requirement for electrical safety is always to place electrical equipment in an electrically safe condition whenever possible through a proper lockout/tagout procedure. But de-energizing electrical equipment is not always possible; NFPA 70E 2009 provides additional best practices for electrical safety during energized electrical work.
Statistics show that a serious injury sustained in an electrical accident will ultimately cost the employer and its insurers between $8 million and $10 million total in direct and indirect costs if the victim survives, and in some cases the costs have been much higher. These costs include long-term hospitalization and medical care, litigation, worker's compensation premium increases, OSHA citations, equipment damage, loss of work in process, business interruption, and other indirect costs.
If the company is not financially strong enough to be able to recover from these financial losses, the company itself could ultimately fall victim to the accident. Managing risk is a very important responsibility for senior management and is fundamental to good business management practices.
Development of the Electrical Safety Standards
Electrical shock hazards have been well documented for many years, and most electrical workers understand the shock hazard and have been well trained to avoid electrical contact injuries. Arc flash and blast hazards were less well known until late 1999, when testing data first became available that allowed for the development of accurate calculation methods. These calculation methods allow electrical engineers to accurately calculate and predict how much thermal energy would be released in an arc flash event based on the condition of voltage, available fault current, device clearing times, and other contributing factors.
Calculation methods and formulas that provide for accurate calculations were first published in a standard called IEEE® 1584 2002, titled Guide for Performing Arc Flash Hazard Calculations. The process of using these calculations and the resulting risk assessment are often called an arc flash hazard analysis. This analysis is now a permanent compliance requirement in the electrical safety standards.
With this new technology available and heightened awareness of electrical safe work practices, electrical workers are now able to better protect themselves with personal protective equipment (clothing and other protective equipment) and other equipment for safe electrical work that is rated specifically for each potential hazard level. This was a significant milestone in electrical safety, and the positive effects of it are being seen every day in the reduction of workplace injuries and fatalities from arc flash events.
But adoption of the compliance requirements by OSHA and in NFPA 70E is far from universally implemented in the private sector even today. The awareness of the electrical safety requirements and arc flash hazards has been widely promoted, but many companies struggle with compliance for various reasons, one of which always seems to be financial.
Elements of Electrical Safety Requirements
Creating a corporate safety culture requires very committed leadership and effective communication of management safety policies and management expectations to all levels of the organization. In order for safety principles to become ingrained throughout the enterprise, management expectations and management commitment must be constantly demonstrated.
It is often stated that "safety doesn't happen by accident." Sometimes, unfortunately, the motivation for business leaders to incorporate a commitment to safety into their business policies does result from a serious and costly accident. Being proactive about implementing safety in your organization is always a better approach than waiting for a serious accident to happen.
Compliance with the electrical workplace safety requirements can be confusing and does involve some costs that probably were not anticipated in the current annual operating budget. Because cost is an element of the electrical safety compliance program, these costs should be anticipated and budgeted in order for the program to succeed.
The following summary lists the basic requirements for electrical safety compliance.
OSHA requires that employers must provide the following:
- Written electrical safety program
- Hazard analysis (arc flash and shock hazard analysis)
- Labeling of electrical equipment
- Specific hazard training for workers in order for workers to be considered "qualified" by OSHA
- PPE for electrical workers
- Tools (insulated hand tools and other specific electrical safety tools for workers)
An adequate preventive maintenance and testing program for electrical equipment
Each of these elements will involve some cost. The hazard analysis will likely be the most costly item to implement, but that cost only occurs once, with minor costs in succeeding years for maintenance and re-verification of the analysis when conditions change in the facility's electrical systems.
Labeling of electrical equipment is based on the values that are calculated in the hazard analysis, and equipment labeling is offered by many qualified vendors as an option to the proposal for the arc flash analysis. The labeling cost is only a small percentage of the overall hazard analysis cost, and it is basically a one-time cost.
The cost of PPE and safety tools will depend on many factors, including the number of employees who need the equipment. Most companies get the analysis done first, then choose PPE and tools based on the specific hazard conditions unique to their specific facility electrical environments.
Worker training is probably one of the most cost-effective requirements to effectively reduce risk. This training is required of every employee who performs work on electrical equipment. OSHA will not recognize that any employee is qualified to do electrical work unless this training has been provided for him and documented.
Points to Remember
Electrical accidents that injure or kill a worker are never caused by intentional acts. Accidents happen because workers are unaware of the hazards and how to protect themselves from them. There is a very high element of human causation, and in almost every case, electrical accidents are caused by some unsafe act by a worker. Worker training is also offered by many companies and is quite inexpensive compared to its effectiveness as a risk management strategy.
The case for investing in safety is clear when compared with the potential risk of losses. Investments in electrical workplace safety are fundamental to good business management. Statistics indicate that investments in safety programs will return about $4 to $6 for every dollar spent. The direct and indirect cost of a serious accident with OSHA citations is extremely high in both human and financial terms.
Decisions must be made, communicated, and directed by the executive leadership in order for them to become effectively ingrained as a safety culture in your facilities. Commercial assistance is available to advise on compliance and provide the required elements.
The safest practice is to avoid all work on energized electrical components whenever possible. But when the work must be done while equipment is energized, safety practices must be followed to protect the employee and the employer. Making and communicating that decision is only the first step in an overall risk reduction safety strategy.
The market value of an employer's reputation for safety is incalculable. Electrical workplace safety is a very serious matter, and we hope this short introduction will help to promote awareness of your responsibilities in this matter.
This article originally appeared in the September 2011 issue of Occupational Health & Safety.