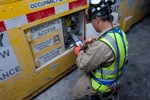
Three Things Every Industrial Hygienist Should Know About Gas Monitoring
Of course, workers cannot be properly protected from exposure hazards if they are not regularly using the monitors intended to detect the hazard.
- By Dave D. Wagner
- Oct 01, 2012
Industrial hygienists are at the forefront of health and safety in today’s industrial workplaces. Their focus runs deeper than the everyday safety issues that involve hard hats, safety glasses, fall protection, and lockout/tagout scenarios. Their emphasis is pointed toward the health side of health and safety, where they spend considerable effort ensuring workers in their environment are protected from hazards that may represent immediate and long-term effects on their general health and well-being. They study and work to control worker exposure to hazards such as noise, dust, and, of course, gas and vapors.
As part of being responsible for controlling the hazards themselves, the IH becomes responsible for managing the programs and tools used to monitor the hazards. When it comes to gas detection, there are three things that all industrial hygienists need to know about their gas detection instruments in order to manage a complete exposure program. They must know that their instruments work properly; that they are used properly; and, finally, they must gain clear understanding of the hazards to which their workers are exposed.
An accurate worker gas exposure assessment requires a detector that is working properly. To maintain and provide accuracy, gas monitors must be calibrated regularly. In the past, this was so important to most industrial hygienists that gas monitors were calibrated just before being used for making exposure studies and then again, just after the particular study is completed, to ensure the integrity of any data collected. Although this level of calibration is not necessary in most applications today, it is still very necessary to know that gas monitors are being maintained through calibration on a routine basis.
While most industrial hygienists would agree that calibrating monitors before each use is no longer necessary to ensure accuracy, they also would agree that verifying functionality before each use is. In today’s gas monitoring programs, industrial hygienists no longer have personal control of all the monitors that are in use. Still, they must have assurance that those monitors are functionally ready to go at all times. The only true way to know that a gas detector will respond to a hazardous gas concentration when it is presented with one is to actually challenge it by exposing it to the target gas. This is a fact that is not well known. As such, industrial hygienists and other safety managers must know that the detectors are bump tested and functionally validated prior to each time they are used.
Ensuring Proper Use
Having assurance that gas monitors are being properly maintained is a big first step to having a good program, but industrial hygienists must have similar assurances that the monitors are being used properly.
First, they must be able to verify routinely that monitors are used when and where they are expected to be. Workers cannot be properly protected from exposure hazards if they are not regularly using the monitors that are intended to detect the hazard. They also must know that workers respond properly to the warnings that the monitors provide. A workforce driven by the responsibility for getting the job done may not pay attention to warnings and dangerous conditions, putting completion of the task at hand ahead of their own safety. In many cases, workers have been known to blatantly ignore alarming gas monitors by simply turning them off so they can continue to work without the annoyance of the detector. Industrial hygienists and others responsible for managing monitoring programs and ensuring worker safety must be able to uncover these cases.
More important than knowledge of the maintenance and use practices surrounding their gas monitoring instruments, industrial hygienists must have an understanding of the conditions and hazards that workers are exposed to on a daily basis. They must be able to uncover when and where these conditions exist in order to mitigate them effectively. Many industrial hygienists have expressed the need to see an employee’s peak exposure and track TWA exposure levels every day. These and similar requirements fall within the primary responsibility of many industrial hygiene professionals.
IH Data in the Cloud
All of the information outlined here lies within the data contained under the covers of gas monitoring instruments and systems. The key to obtaining and understanding the data is having a strong gas monitor management system. The system should not only be able to automate the routine tasks of instrument calibration and bump testing, but also it should be able to recover critical exposure data from within the monitors and generate warnings and reports that alert the personnel who are responsible for managing the program when use scenarios and hazard conditions are not at optimum levels.
Remote work scenarios and global responsibilities mean that this information must be able to be recovered and reviewed from anywhere in the world. This makes the ability to manage and maintain a gas monitoring program within "the cloud" a critical feature of any system. Industrial hygienists should be able to use today’s technology to access data and manage tools that are critical to their job functions in the same way they manage other aspects of their everyday lives.
Evidence strongly suggests that industrial hygienists and other safety personnel who have access to data from their gas monitoring programs in this manner, and review it regularly, have fewer gas alarm events and higher safety levels than those who don't.
As long as workers have the potential to be exposed to gas hazards in their work environments, there will be industrial hygienists who have the responsibility to understand and mitigate those conditions and manage the programs and tools used to detect them. Using a service that allows them to know their equipment is ready to use, is used properly, and identifies the actual conditions that exist will ensure they can effectively manage and maintain the health and safety of the workforce.
This article originally appeared in the October 2012 issue of Occupational Health & Safety.