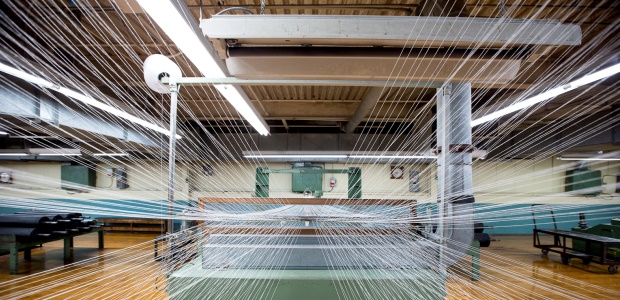
Vertical Manufacturing of Flame-Resistant Cotton and Cotton-Rich Fabrics
Wear trials can help guide you in selecting the right fabric by providing a more comprehensive evaluation of important factors such as performance, comfort, and applicability.
- By Craig Tutterow
- Dec 01, 2015
A recent study of 400 SH&E professionals found that 71 percent agreed that it is important to specify the fabric used in the flame-resistant clothing for their workers. In order to know what to look for in choosing a flame-resistant fabric, you should be knowledgeable on how they are made, because the more you know about flame-resistant fabric, the more confident you can be in the comfort, durability, and performance of your FR clothing.
Every flame-resistant garment begins with flame-resistant fabric, but it's important to fully understand how and where the fabric is produced. Some companies buy base materials, or greige fabric, for use in producing their flame-resistant fabrics, which means they are buying unfinished fabric from a third party. In contrast, companies that are vertically integrated manufacture their own greige fabric, often resulting in a more consistent fabric weight, width, dye shade, and color retention and, overall, a higher level of reliability. When deciding whom to buy flame-resistant fabric from, consider this: When a company buys rather than manufactures greige fabric, how can it know for sure how the fabric will respond? Companies that apply an FR treatment to fabric purchased from multiple sources run the risk of two fabrics not dyeing the same or reacting the same to the FR process. In fact, it can be very difficult to dye and finish fabric from multiple suppliers and produce a fabric with consistent width, weight, shrinkage, shade, and color retention.
The major steps in manufacturing are fiber selection and blending, yarn formation, weaving, dyeing, FR treatment, and finishing. Opening and blending are the first steps in yarn formation, where bales of cotton are selected and blended together to optimize yarn quality and strength. U.S.-grown cotton is among the highest quality in the world, and it is tested and classified by the U.S. Department of Agriculture for important properties that include fiber length, strength, fineness, color grade, trash, and leaf grade. The opened fiber is then moved into carding. In the carding process, foreign matter and short fibers are removed from the cotton. The cotton is then consolidated into a loose strand called sliver. The sliver then moves to spinning, where the drawn-out strands of fibers are twisted together to form yarn and wound into packages.
Packages of spun yarn are then loaded onto a creel, and the yarn is wound onto a section beam for slashing. This beam of yarn will eventually be placed onto a loom, which is where the fabric will be produced. Multiple slasher beams are combined in slashing to form the loom beam that will be woven into fabric. The slashing process coats warp yarns with a mixture called sizing to protect and lubricate the yarns during weaving. Starch and a lubricant are the traditional materials that are used for warp size to improve weaving performance and fabric quality.
Next in the process comes weaving, where yarn is woven into fabric. Flame-resistant fabrics can be made more consistent by weaving them on the same looms with the same construction, yarn tension, weft insertion rate, reed width, and off-loom width. All of these factors must be consistent to produce fabric with the same physical properties and performance.
After the fabric has been woven, it goes into wet processing. Each step in wet processing builds on the previous step, beginning with preparation. Preparation may include singeing, desizing, scouring, bleaching, and mercerization. Fabrics are singed to burn off loose or long fibers in order to create a smooth surface and reduce fabric pilling during wash and wear cycles.
Good preparation starts with desizing to remove the corn starch and lubricating agent that were put on prior to weaving. This is an extremely important step in producing a fabric that dyes and responds to FR treatment properly and consistently. Because a vertically integrated manufacturer knows exactly what has been applied to the warp before weaving, it knows exactly how to remove it during the desizing step, leading to more reliable fabrics.
Bleaching typically uses hydrogen peroxide to increase the fabric whiteness, while mercerization is a treatment with sodium hydroxide to improve the absorbency, luster, reactivity, and dyeing properties of a cotton fabric. Proper mercerization is key to producing a fabric with durable flame resistance.
The dyes belonging to the class known as vats have the best wash and lightfastness for cotton and cotton-rich fabrics, so they are the first choice for dyeing flame-resistant fabrics.
Durable flame resistant fabrics are produced by a carefully controlled reaction that takes place within the fabric. Properly prepared fabric is saturated with THPS (Tetrakis Hydroxymethyl Phosphonium Sulfate) precondensate. Then the fabric with THPS is partially, but not completely, dried and moved through the ammonia (NH3) chamber. Nitrogen from the ammonia gas polymerizes the THPS within the fabric, yarn, and fiber; and the THPS polymer also cross-links with the cellulose. Subsequent oxidation with hydrogen peroxide converts the THPS from a tri-valent to a penta-valent polymer. This flame-resistant finish polymer lasts for the life of the garment.
Once a fabric has been manufactured, it should be inspected and tested for quality assurance and to ensure that the fabric meets or exceeds the ASTM and NFPA standards for flame resistance.
Specifying FR Fabrics
Understanding how flame-resistant fabrics are made should help you choose a manufacturer, but before you specify the fabric for your FR clothing programs, consider that the best way to determine the optimum fabric is through a properly executed wear trial. Wear trials can help guide you in selecting the right fabric by providing a more comprehensive evaluation of important factors such as performance, comfort and applicability. To ensure that the trial is conducted properly and provides consistent feedback, the following "best practices" should be considered in your wear trial:
- Limit the number of fabrics and/or garment styles to minimize confusion.
- Do not involve too many employees, but consider using some from different shifts and areas to ensure consistent feedback across the organization.
- Use standard questions and ranking scales (e.g., 5-point Likert scales) to obtain measurable feedback.
- Allow for the evaluation of fabric and garment construction separately—did they like the fabric but not the garment, or vice versa?
- Ask for written comments to add context to the data.
Following these practices should help guide you in selecting the right fabrics, which is very important in helping you have the right flame-resistant clothing for your needs and environment.
This article originally appeared in the December 2015 issue of Occupational Health & Safety.