Chemical Protective Clothing: Navigating Standards to Match Your Hazards
You should strive to select the best CPC for worker protection.
- By Susan Lovasic
- Jul 15, 2019
In the USA, general industry employers have regulatory responsibility for selecting Personal Protective Equipment under OSHA 29 CFR 1910.132. Employer assessment of workplace hazards drives the selection of appropriate PPE. Only respiratory protection is required to be approved by a government agency in the USA—specifically by the National Institute for Occupational Safety and Health (NIOSH); however, other types of PPE available for consideration and selection may be third-party certified. It is important that safety professionals understand details of key certification standards to make informed decisions when matching PPE to their workplace hazards. This article will focus on chemical protective clothing (CPC) testing and National Fire Protection Association hazardous materials (hazmat) standards that can be used to assess chemical PPE.
CPC Assessments—A Sum of the Parts
The performance of CPC, in terms of chemical barrier protection, durability, and hazard scenario suitability factors, can be assessed at several levels: the material, seam, closure system, and finished garment.
The suit material's chemical barrier protection level is best quantified using the ASTM F739 permeation test and the suit material’s physical properties should also be measured to predict durability. Likewise, the chemical barrier and physical strength of seams used to join the material to create a garment should be evaluated. For most applications, the seam should be sealed and provide a barrier level at least equivalent to the garment material.
The closure system of the garment should be considered for suitability based on the hazard scenario. The suit closure area can be the weakest link in the garment, and safety professionals must consider whether it will provide effective barrier against the particles, liquids, and/or vapors in their hazards. It is very common for the closure system—most often a specialized zipper—to be covered by an extra flap of garment material that is secured in place, to provide an extra layer of protection.
In addition to tests run on materials used in garments, full garment testing can be conducted to assess robustness of the garment design. These tests most often check the suit's ability to hold out a specific phase of non-hazardous chemical (particle, liquid, or gas). The chief failure mechanism for a full garment test is penetration through a void or defect or poor seal at an interface. A "passing" rating in these full suit tests does not mean that the suit is 100 percent impervious to all hazardous chemicals of the same phase. Rather, these tests can be used to identify weaknesses in the garment design that permit leakage into the suit of challenge particle, liquid, or gas chemicals.
Full suit test methods are provided in various ASTM, ISO, and EN standards. There are a variety of tests to assess suit "liquid integrity." These tests chiefly vary in how they expose the garment to the liquid and the surface tension, volume, and/or pressure of the test liquid water. The common methods are described as a Shower test, Jet test, Spray test, or Mist test. The liquid integrity test method used is based on the targeted hazard application of the suit. There are also tests to check the inward leakage of a gas/vapor or of small particles into the suit. Full garment/ensemble tests are excellent ways to assess the robustness of garment design, components, and interfaces of a PPE ensemble.
Matching Certified Suits to Hazards
A common question during the CPC selection process is, "Will a certified suit be the best match for my hazard?" The answer to this question is, "It depends on the specific standard and your specific hazard scenario." Each CPC standard has strengths and limitations to consider to determine whether or not a certified garment would match the protection level needed.
A strength of certified CPC is that performance requirements were developed using a consensus process. Additionally, when the CPC is third-party certified, the certifying agency provides oversight to the CPC manufacturer. There are, however, some limitations for CPC performance standards that should be considered. First, every standard has a very specific scope for how the CPC is evaluated and its intended use. Care must be taken to understand the level of protection the suit is designed to provide. Additionally, standards use a specific limited battery of hazardous chemicals to test the suit material and components. This raises the dilemma—is a third-party certified garment the best choice if it was not tested against the chemical hazards identified in your hazard assessment?
Because of this, unless certification of CPC is required by your employer or government regulation, whether or not CPC is certified should not be the only question you ask. Rather, you should start with the hazard assessment and find CPC that will protect against your specific hazards. Ideally if the CPC meets your hazard protection needs and is also third-party certified, then certification of the CPC will add extra value to protecting your workers.
Comparing NFPA 1991, 1992, and 1994
For CPC used in the USA, several key certification standards are published by the NFPA. There are currently three main NFPA standards covering hazmat PPE. These standards are NFPA 1991,1 1992,2 and 1994.3 NFPA 1994 offers seven unique classes within the standard, so in all there are nine possible varieties of NFPA-certified suits for hazmat PPE. The "R" designation after NFPA 1994 Classes 2, 3, and 4 is used to denote a "ruggedized" version of each; they have higher physical strength requirements but use the same chemical barrier requirements as the non-ruggedized versions. This article will highlight key differences to help determine whether a garment certified to a particular NFPA hazmat standard will offer the appropriate level of protection for the chemical hazards identified in your assessment.
Each NFPA hazmat clothing standard covers a different scope or purpose and therefore uses different tests and requirements. When deciding whether a CPC item certified to a NFPA standard is appropriate for your chemical exposure, it is helpful to understand how certified suits were evaluated. Table 1 provides a high-level overview of the nine options available from NFPA 1991, 1992, and 1994 standards, along with some key performance levels.
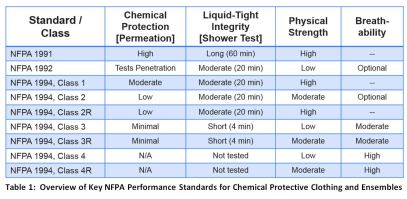
While many of the same tests are used in these NFPA standards, the performance limits vary significantly because of the different scopes and expected performance levels of the suits. For example, all but two of the options require a "shower test" to evaluate liquid tight integrity of the suit/ensemble. But as noted in Table 1, the length of exposure to the shower test varies from 60 minutes to just 4 minutes. This is not surprising since the scope and/or application for these standards are different. For example, NFPA 1994 section 1.3.3 notes (underlines added) that Class 3 protective ensembles are “designed to provide limited protection to emergency first responder personnel at hazardous materials or terrorism incidents involving low levels of vapor or liquid chemical hazards, where the concentrations are below immediately dangerous to life and health (IDLH), permitting the use of air-purifying respirators (APR)."
A Closer Look at Required NFPA Chemical Barrier Testing
There are also differences in how chemical barrier protection is measured. Table 1 lists relative chemical protection levels. NFPA 1992 assesses chemical barrier properties versus 10 liquid chemicals using the ASTM F903 penetration test method. Because NFPA 1994 Class 4 suits are designed only for particulate hazard protection, neither permeation nor penetration material tests are used. There are six NFPA options that do use permeation testing to assess chemical barrier, but there are differences in how stringent that testing is. Table 2 shows details of permeation testing required for NFPA 1991 and NFPA 1994 Classes 1, 2, and 3.
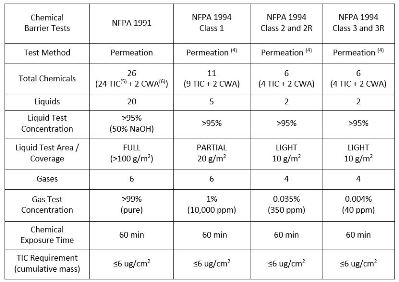
Table 2: Permeation Tests Used to Qualify NFPA 1991 and NFPA 1994 Suit Materials
Notes:
(4) Sulfuric acid for NFPA 1994 is only tested using penetration test, not using a permeation test.
(5) TIC = Toxic Industrial Chemical
(6) CWA = Chemical Warfare Agent
At first glance, it may appear that permeation testing is comparable since the test duration (60 minutes) and the pass/fail requirement (≤6 ug/cm2) are the same. That is not the case. How permeation testing is conducted varies significantly among these standards because of the different scopes and intended performance levels of the suits. First, note the number of chemicals included in the test battery—NFPA 1991 uses 26 chemicals and NFPA 1994 Class 1, Class 2, and Class 3 use 11, 6, and 6 chemicals, respectively. Additionally, note that NFPA 1994 only requires sulfuric acid to be tested using a penetration test, while NFPA 1991 uses the permeation test for all 26 chemicals, including sulfuric acid.
The next difference is that NFPA 1991 uses more liquid challenge chemicals (20) and the liquid volume in contact with the material is the highest. For NFPA 1991, the liquid must fully cover the test specimen for the full duration of the test. For 1994 Class 1, droplets amounting to 20 g/m2 are applied to the material, which only partially covers the sample. For NFPA 1994 Classes 2 and 3, the liquid droplet coverage is limited to just 10 g/m2.
How does gas permeation testing compare? While all require between four and six challenge gases to be tested, NFPA 1991 requires all six gases to be >99% pure. But for NFPA 1994 Class 1, the test gas concentration is only 1% in air. For Class 2, it's only 0.035%. For Class 3, it is very low at 0.004%. So while each of these NFPA standards requires tests be run to measure gas permeation through the protective material, the actual gas challenge used is markedly different.
Note the last column in Table 1 labeled "breathability." For two standards (NFPA 1992 and NFPA 1994 Class 2), breathability is an optional claim. For two others—NFPA 1994 Class 3 and NFPA 1994 Class 4—there are mandatory requirements. Both NFPA options with breathability requirements have lower permeation barrier and/or lower liquid integrity (shower) test requirements. As you might expect, there are usually trade-offs in protection to increase breathability. CPC thermal comfort is clearly a concern to be considered, but it must be balanced with the primary reason the suit is being worn—namely, chemical protection.
Although six NFPA standard options for CPC use permeation to measure chemical barrier, the exposure challenges used for NFPA 1994 are fewer, less concentrated, and therefore less challenging than what is used for NFPA 1991. These differences in standard chemical barrier testing requirements are important for safety professionals to consider to ensure CPC was tested against the chemical hazards (including concentration level) in their hazard scenario.
Summary
Decisions regarding CPC selection will directly impact the health and safety of workers. When selecting CPC, the greater your knowledge of different types of suits available (whether certified or not) and how they were evaluated will improve your ability to find the best match to protect from the chemical hazards of concern. Full garment tests are a good way to assess the robustness of the design, components, and the expected PPE ensemble interfaces. CPC that is certified to an NFPA hazmat standard can offer benefits if the certification requirements match the protection needs identified in your hazard assessment.
The NFPA standard performance levels discussed in this article are the minimum requirements. Nothing in any of these NFPA standards restricts the manufacturer from exceeding these minimum requirements. Therefore, if performance requirements of a suit certified to a NFPA standard do not match your hazard protection needs, further information may be requested from the suit manufacturer to determine whether any additional relevant testing was performed above what NFPA required.
This article originally appeared in the July/August 2019 issue of Occupational Health & Safety.