Bringing Process Safety Management into the Digital Era
Why worry about reporting if you can prevent the release in the first place?
- By Sean Baldry
- May 01, 2020
The regulatory landscape for process industries in the United States became a little more onerous earlier this year. On February 21, 2020, the U.S. Chemical Safety and Hazard Investigation Board (CSB) released its final rule outlining new reporting requirements for facilities that suffer accidental releases of highly-hazardous chemicals.1
The new rule sets out stringent timelines for reporting accidental releases of hazardous chemicals that result in serious harm to persons or extensive environmental damage. It also outlines the specific information that must be released to the CSB at the time of the report. Organizations that fail to meet these new reporting obligations could face stiffer regulatory enforcement, including citations and fines.
While the new rule came into effect on March 23, 2020, CSB announced that it would provide the industry with a one-year grace period, so businesses could make the necessary changes to their operations in order to meet these new requirements, before active enforcement begins.
It’s understandable that, in light of these changes, process facilities will focus their efforts on updating their reporting workflows and emergency response protocols, so they’ll be able to comply with the rule if, and when, such a release occurs.
But companies would be better served to instead use the time available to assess whether their entire Process Safety Management (PSM) system is effective enough to detect and control potential process failures before they result in harmful releases. Why worry about reporting if you can prevent the release in the first place? Remember the adage: an ounce of prevention is worth a pound of cure.
Prevention is the Best Medicine
PSM’s main purpose is to prevent unwanted releases of highly-hazardous chemicals. When properly designed, well implemented and rigorously maintained, PSM programs provide organizations with vast capacity to control risk, while building resiliency that enables the system to adsorb “shocks” without it resulting in catastrophic failure.
So then why do hazardous releases continue to occur?
Organizations that struggle to maintain effective PSM programs are often challenged due to a confluence of factors: highly-complex processes, a lack of technical and process risk expertise, the speed and scale of process changes, conflicting priorities, and a lack of resources to manage system outputs. Without solutions to manage these variables effectively, businesses are on borrowed time, and the potential for highly dangerous releases becomes more of a question of “when” than “if.” It’s critical that employers begin to invest in solutions that will help them manage this burden, while keeping them competitive.
Enhancing your PSM Capabilities with Technology
Organizations that leverage software to assist in managing process safety are better positioned to limit their operational risk exposure, prevent potential accidental releases and achieve regulatory compliance. But how specifically does software help? Let’s take a quick look at three of the most critical steps in your PSM process—process hazard analysis, management of change, and pre-startup safety reviews—and discuss how adopting a digital approach to PSM can help to effectively reduce the risk of unwanted releases.
Process Hazard Analysis
The ability to effectively mitigate risks posed by hazards within any complex system starts with identifying where, why and under what conditions those hazards may arise. A Process Hazard Analysis (PHA) refers to the thorough, orderly and systematic approach to identify, evaluate and control process-related hazards involving hazardous chemicals.
But completing a PHA is not the simplest of tasks. N. Hyatt describes it as “the industrial equivalent of a trip to the dentist—usually arduous and painstaking.”2 For organizations seeking to realize full value from PHAs, they need to discover ways of making the process easier to complete. Two of the biggest issues with completing PHAs is coordination and consistency.
In advance of any analysis, relevant process safety information that describes the hazards posed by equipment, technology or the products themselves needs to be collected. Software solutions that enable users to easily assemble equipment inventories and process flow diagrams are particularly useful during these data-gathering exercises. Solutions that afford access to managed SDS libraries enable key chemical information—from toxicity or reactivity data to exposure limits—to be included directly in the analysis. This coordination of data is invaluable as it provides PHA teams with the right information to make informed judgments on risk.
Most PSM standards do not dictate the specific way in which a PHA must be performed. Instead, they require that employers select a PHA methodology appropriate for the complexity of the process, from what-if analyses to HAZOP and FMEA. These tools can be quite challenging to navigate, especially for those who do not complete them regularly.
Intuitive tools built into many software packages are designed to simplify and streamline the PHA task. Built-in menus and configured calculations within selected PHA methodologies save time by reducing confusion, while also decreasing simple data-entry errors that could lead to an underestimation of risk. Workflows with integrated notifications ensure PHAs are reviewed regularly, according to regulatory timelines, so they are always up-to-date. However, the true benefit of software comes from its ability—with advanced analytics and business intelligence tools—to identify and track patterns of risks across operations. Such data provides clear actionable insights that better enable organizations to prioritize what needs to be done to reduce the chance of process failure.
It’s often forgotten is that PHA is a team-based exercise. Since front-line workers are the individuals who actively manage these critical processes on a daily basis, their feedback is essential to understand the risks and how best they can be controlled. Yet, workers are often excluded from PHAs, which itself can contribute to disaster. Such a lack of participation was cited by the CSB during their investigation of a fatal explosion at a petroleum refinery in Washington state in April 2010, which cost the lives of seven workers.3
Employee engagement is a key ingredient in developing robust safety cultures critical for operational excellence.
Software offers a unique vehicle to engage workers in process safety. Mobile apps now allow workers to view completed PHA’s directly from a mobile device, as well as initiate process change requests, report chemical releases, or even track related actions to help drive closure and accountability. By providing easy access to highly visual PSM data from a mobile device, organizations can strengthen perceptions of transparency and trust between leaders and the workforce, ensuring that everyone is knowledgeable of and contributing to effective process safety management.
Management of Change
Change in business is a constant. Well-executed change can improve productivity, quality and morale. Poorly-managed change not only creates inefficiency and added costs, but it can also lead to catastrophe.
That’s exactly what happened on June 13, 2013. That morning, a maintenance crew at the Williams Olefins petrochemical facility, located on the outskirts of Baton Rouge, La., were responding to an issue with a reboiler on the propylene production line. The workers involved at the time decided to restart a standby reboiler to allow production to continue as they worked to resolve the problem. These workers were unaware, however, that as part of taking the reboiler offline months prior, the propane fuel system feeding the equipment had been isolated from its pressure relief valve. As hot water was re-introduced to the system, the gas pressure from heating the liquid propane mixture inside the reboiler rose to almost 1,200 psi. The pressure caused the vessel to rupture and ignited a massive gas explosion. Two workers were killed in the explosion, and nearly 200 others suffered injuries.
In their subsequent investigation, CSB described a deficient safety culture at the plant, which they attributed to multiple process safety management failures in the years leading up to the event. Particularly, the CSB focused intently on process changes that had occurred over 10 years prior, in which the company “failed to appropriately manage and effectively review two significant changes that introduced new hazards involving the reboiler.”4 A CSB spokesperson later remarked that engineers had failed to identify scenarios where the absence of the pressure-relief valve could have introduced unintentional hazards.
The event exemplifies perfectly how vital management of change is to process safety. Yet most organizations struggle with change management at the best of times, often because they lack a well-designed and repeatable workflow to review changes, consider their impacts and ensure actions necessary to mitigate impacts are completed before the change can occur. To complicate matters, paper-based Management of Change processes that rely on individuals to initiate and track changes are subject to human error, forgetfulness, complacency and competing priorities, each increasing the risk of unapproved change squeaking through unnoticed.
Creating that integrated workflow is perhaps the chief benefit of shifting to a digital change management process. Software solutions optimize our ability to manage change by providing a reliable platform within which prospective changes can be prioritized, review and assessed. Based on the type of change considered, distinct actions within the change workflow—whether process hazard analyses, development of operating procedures, updates mechanical integrity inspections or worker training—can be automatically assigned and tracked. As a result, employers have greater assurance that crucial validation steps in the change workflow aren’t missed or skipped, driving process accountability. Integrated notifications and alerts based on task status available in most software solutions also enable prompt escalations without relying on individuals to initiate them.
While we cannot be certain, one could argue that a digital solution may have assisted Williams Olefins identify potential risks posed by reboiler over-pressurization at the earliest stage in the change process, and may have prompted the consideration of additional safeguards, which may have helped prevent tragedy.
Pre-Startup Safety Review
A final step in bringing any new facility online or executing any process safety change involves a pre-startup safety review. Yet, organizations facing budgetary pressures and time constraints often forego this “last chance” opportunity to assess operations and mitigate potential impacts since they’re too focused on getting the new process up and running. But skipping that review can lead to trouble.
In 2005, a defective pressure control valve in a distillation tower at BP’s Texas City refinery led to a flammable liquid explosion that killed 15 workers and injured nearly 200, resulting in $1.5 billion in financial losses for BP and extensive property damage within a one-mile radius of the plant. The investigation assigned the incident, in part, to the fact that the ISOM unit start-up following a maintenance turnaround was “authorized despite having inadequate staffing, malfunctioning instruments and equipment, and without a pre-startup safety review.”5
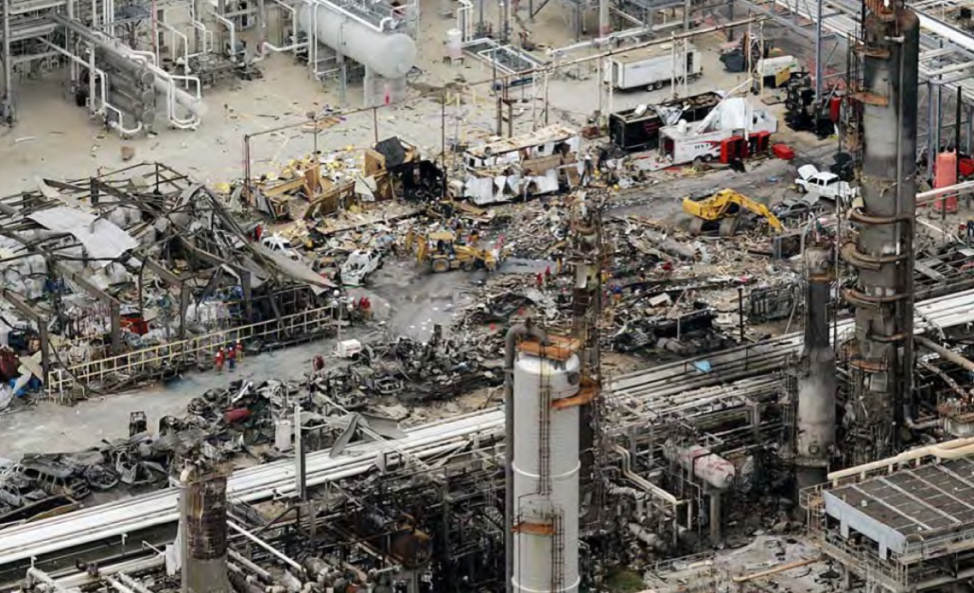
Aftermath of the BP Texas City refinery explosion in 2005.
Pre-startup safety reviews are employed to verify that:
- Equipment is installed, and structures are constructed in accordance with good engineering design;
- Adequate operating, maintenance, safety and emergency procedures are in place;
- Process Hazard Analyses have been conducted and recommendations arising from those analyses have been resolved; and
- Workers have been appropriately trained.
Ensuring that all these steps are completed is difficult enough for a single change. But changes are not always sequential. Many occur concurrently with others, which makes keeping track of the status of all tasks within a pre-start review process particularly challenging. Software provides tools to help simplify this necessary oversight.
Many mobile applications6 allow companies to create digital checklists and questionnaires that help ensure key elements are considered as part of the pre-start evaluation. Where an element is recorded on the checklist as out-of-compliance, integrated workflows can automatically trigger and assign corrective actions to key stakeholders, which can then be monitored and verified for completion before final approval for the change is given. Such enhanced oversight ensures that costly delays are avoided, and that organizational leaders can remain informed of the status of operational readiness. Moreover, enhanced analytics features in software solutions can help users discover patterns of common failures or deficiencies across processes, departments or locations, which can serve as a database of “lessons learned” that can be used when bringing future systems online.
Think Simplicity
Suffering a release of highly hazardous chemicals does not simply mean more reporting. Beyond the risk to human life, it can disable operations and fatally damage brand reputation that is critical to maintain a social “license to operate.” Process safety management is inherently challenging based on its complexity. To manage process risks effectively, organizations need to explore ways to simplify how to do it. Those able to do so will be much better positioned to reduce the risks to their workforce, and the surrounding community.
REFERENCES
1 https://www.ishn.com/articles/112236-csb-finalizes-chemical-incident-reporting-rule
2 Hyatt. N. 2000. Computer software for process hazard analysis. Journal of Occupational Health and Safety. 68(10): 188-192.
3 https://isssource.com/lack-of-worker-participation-led-to-refinery-disaster/
4 https://www.csb.gov/williams-olefins-plant-explosion-and-fire-/
5 https://www.csb.gov/file.aspx?DocumentId=5596HYPERLINK "file:///Users/1105admin/Downloads/CSBFinalReportBP.pdf"
6 https://www.ehstoday.com/safety/article/21917785/a-poor-process-safety-culture-at-williams-olefins-plant-contributed-to-the-2013-explosion-that-killed-two-employees
This article originally appeared in the May 2020 issue of Occupational Health & Safety.