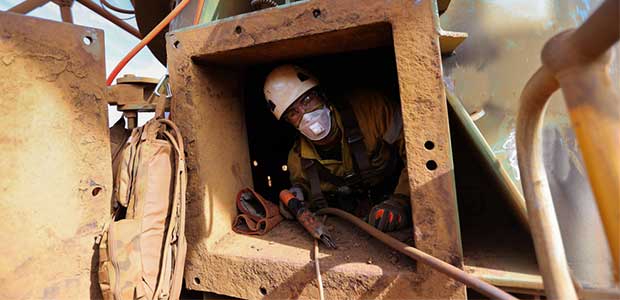
Entering the Alligator Pit: An Overview of Confined Space Standards
Confined spaces continue to put workers in hazardous situations. It is crucial to identify hazards and design procedures to protect.
- By Tom Burgess
- May 01, 2021
A worker once said in frustration, “If we had three different safety people in here, they would all give us a different answer.” I’m sure this is likely not the first time you have heard this type of comment, but it certainly isn’t something you want to hear when you are discussing a worksite’s confined space entry procedures. In any situation where lives may be at risk, it is important that workers know exactly what to do to keep themselves and each other safe.
On the other hand, confined space safety does not conform to a one-size-fits-all approach, and in some circumstances, the “conventional” requirements can be unnecessarily burdensome. For this reason, we don’t treat every confined space the same. Instead, in accordance with OSHA and ANSI standards, we strive to make sure that our rules are appropriate to the level of risk—that we identify the hazards for each space and situation and control them.
Let’s take a closer look at the standards for confined spaces and the importance of knowing what hazards exist so that we can control them. This will enable you to get work done while achieving the top priority of preventing anyone from being hurt or worse.
What is a Confined Space?
In a nutshell, OSHA’s definition of a confined space covers spaces that are large enough for the entire body of a person to enter and perform work, that are difficult to enter and exit, and that are not designed for continuous human occupancy. Confined spaces may include water or chemical tanks, silos, vaults, tunnels, ductwork, crawlspaces, and manholes, to cite just a few examples. Very small spaces, like a small pump pit that cannot be fully entered by a person, would not be considered a confined space because they do not pose the same hazards. For example, if an employee cannot fully enter a space, they won’t face the same difficulties withdrawing from it in an emergency.
While the ability to enter and exit a confined space without restrictions is not the only safety factor under consideration, it is certainly an important one. The ANSI/ASSE Z117.1-2009 Safety Requirements for Confined Spaces, for example, define a “restriction” as anything that requires the use of the hands for support or the contortion of the body to enter or withdraw from a confined space. Being able to walk through a doorway or large portal is one thing, but if an employee needs to exit a space quickly, and is impeded by a ladder, hatch, or pipes that must be ducked under, that is another story. Especially if a person has been injured or the space is rapidly flooding, or filling with fire or hazardous gases, or some other emergency is present.
Another factor in confined space standards concerns whether a space is designed for continuous occupancy. Just because a space is small and cramped, does not necessarily mean it is a confined space. If it has adequate lighting, mechanical safeguards in place, and—most importantly—a ventilation system, then it may not be classified as a confined space. The OSHA standard gives a vented telecommunications vault as an example of a workspace that may actually be designed for continuous human occupancy. Such a vault will typically be large enough for the worker to stand and move about in, and proper ventilation will be in place to ensure a supply of breathable air and quickly disperse any flammable gases or other hazardous vapors that may be introduced. According to OSHA, atmospheric hazards are the leading cause of injuries and deaths related to confined spaces.
Knowing the Hazards
When it comes to identifying the hazards in a confined space, use the analogy of an alligator pit. Before going into a situation, you need to know whether alligators are present, and then eliminate the alligators. However, that only works if you know where the alligators are, and what they look like.
True story: A contractor requested approval to enter a storage tank to perform work at a chemical plant. They had an entry permit already secured, but they had not yet been informed what had been stored in the tank. They had not even bothered to ask.
How can you already have a plan or entry permit in place, if you don’t even know what had been in the tank? The contractor had a meter to test the air, but what if there had previously been a corrosive chemical in the tank? The air might have been fine, but skin contact with surfaces in the tank could have been very dangerous. Only rinsing out the tank and performing a PH test would confirm whether hazardous chemicals were present.
On the other hand, there was a municipal water utility that had the same rigorous protocols in place across the entire organization, regardless of the hazards in each individual space. Whoever wrote the confined safety procedures made the requirements for every water meter or pump vault the same as they would for a chemical tank.
This can be problematic for two reasons. Firstly, because if you have a pump that is broken and affecting the water supply, and your safety procedures are too burdensome, then you are adding pointless delays that are impacting your customers and business. But even more insidious than this: if your confined spaces protocols are unnecessarily complicated, and your workers know (or believe they know) that certain hazards don’t exist, then they may become complacent, and you can lose workers’ trust in the helpfulness of the rules. I have seen this come up again and again. It is vital that training programs exist to make sure that workers fully understand both the risks and the required controls for each situation. Without this knowledge, workers will assume you are “crying wolf” and may eventually fail to heed a critical and necessary safeguard—with disastrous results. This is why it is crucial to identify only the hazards that are, or may be, present, and have your procedures fit those specific hazards.
For a deeper and more comprehensive dive into this topic, I encourage you to read the OSHA and ANSI standards yourself, and to review the protocols at your particular worksite. Remember that confined space entry requirements will vary greatly, based on the presence or potential for hazards in the space, and whether the hazards can be controlled. Ask yourself: are we aware of all the confined spaces hazards, and are we putting the right measures in place to control them? Does our program distinguish between types of spaces and entry, including permit-required and non-permit required, or alternate entry procedures? Are our workers trained to understand what risks exist, and why these protocols are necessary to mitigate them?
Safety precautions can often seem onerous, especially for workers who are very accustomed to a particular type of work and have been doing it for years without incident. But compare taking appropriate precautions to wearing a seatbelt. You might drive every day for twenty years, and never actually need one. But then, the one time you get into a horrific accident, you’ll be very glad you strapped in.
This article originally appeared in the May 1, 2021 issue of Occupational Health & Safety.